- Amunicja bezołowiowa
- Badania technologiczne wkładki kumulacyjnej
- Badania spieków ciężkich
- Badanie dynamicznych właściwości mechanicznych
- Inżynieria odwrotna
- Opis stanowiska Badań
- Zakres pracy badawczej statutowej (PBS) prowadzonej w Zakładzie
- Badania metalograficzne przewodów luf wykonanych z różnych stali
- Badania trwałościowe oraz monitorowanie przebiegu zuzycia na stanowisku z kamerą i boroskopem
- Opracowanie przyspieszonych metod oceny trwałości luf wykonanych z nowych materiałów
- Pociski kompozytowe do ćwiczebnej amunicji strzeleckiej
- Prasowanie na gorąco rdzeni do pocisków naboju 9×19 parabellum
- Pracownia badań właściwości mechanicznych materiałów w warunkach dynamicznego obciążenia
Amunicja bezołowiowa
W ostatnich latach XX wieku w technice pojawiły się nowe materiały zastępujące ołów w użytkowanych i nowo konstruowanych wyrobach przemysłowych. Tymi materiałami są stopy lub kompozyty, w których zazwyczaj nośnikiem masy jest wolfram z metalicznymi dodatkami stopowymi lub innymi składnikami spełniającymi rolę lepiszcza. W wielu krajach podjęto także, i zakończono z sukcesem, próby zastąpienia ołowiu w pociskach pistoletowych i karabinowych (rys.2). Stosowane są w nich różne materiały, wśród których najbardziej obiecujące są kompozycje zawierające wolfram i cynę (W – Sn).
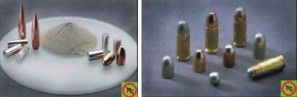
Stosuje się różne technologie wytwórcze rdzeni lub półfabrykatów pocisków bezołowiowych, do których między innymi należą: odlewanie, formowanie wtryskowe kompozycji metalowo-polimerowych oraz metalurgia proszków. Do wytwarzania kompozycji proszkowych wykorzystuje się uproszczone procesy metalurgii proszków, w których konsolidacja składników mieszanki proszkowej następuje w fazie prasowania. W Zakładzie Technologii i Eksploatacji Uzbrojenia podejmuje się próby opracowania technologii wytwarzania pocisków bezołowiowych metodami metalurgii proszków. Dotychczas przeprowadzono badania technologiczne dotyczące pocisków z kompozycji proszkowych miedź-cyna oraz wolfram-cyna. Ponadto dokonano wstępnych badań balistycznych otrzymanych pocisków pistoletowych. Ogólnie proces technologiczny wytwarzania rdzeni lub gotowych pocisków pistoletowych przebiega następująco: po przygotowaniu naważki proszkowej (głównie na drodze mieszania w młynkach planetarnych), zasypywano przestrzeń zasypową matrycy do prasowania proszków (rys.3).
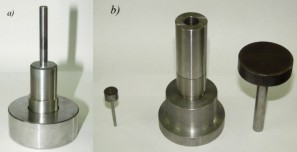
Następnie otrzymane wypraski wygrzewano w odpowiedniej temperaturze, w której zachodziły procesy spiekania powodujące zwiększenie własności mechanicznych pocisków. Ostatnią operacją procesu technologicznego wytwarzania pocisków pistoletowych było przeprowadzenie obróbki wykończającej mającej na celu nadanie ostatecznego kształtu wyrobowi. W wyniku takiego procesu technologicznego otrzymano pociski, które następnie poddane zostały operacji montażu z łuską naboju 9×19 mm Parabellum (rys.4)
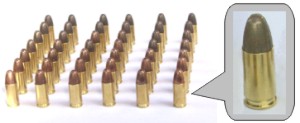
z kompozycji proszkowej Cu-Sn
Z wykorzystaniem tak przygotowanych naboi przeprowadzono badania balistyczne mające na celu sprawdzenie zachowania się pocisku na torze i podczas zderzenia z tarczą (rys.5).
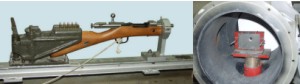
W wyniku badań stwierdzono, że właściwości balistyczne pocisków ze spieku Cu-Sn nie odbiegają w dużym stopniu od pocisku bojowego (z wyjątkiem prędkości początkowej), dzięki czemu mogą być wykorzystane do szkolenia strzeleckiego żołnierzy. Ponadto, stwierdzono bardzo korzystne zachowanie się pocisku po zderzeniu z tarczą wykonaną z blachy 2 mm, które polegało na tym, iż pocisk w wyniku zderzenia ulegał fragmentacji na elementy, których masa w większości nie przekraczała 0,5 g (rys.6).
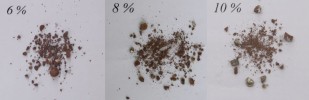
Powstały efekt fragmentacji pocisku z tarczą jest szczególnie pożądany ze względu na bezpieczeństwo strzelań, gdyż fragmentacja pocisku zapobiega rykoszetowaniu i w bardzo dużym stopniu zmniejsza tzw. strefę rażenia pocisku.
Badania technologiczne wkładki kumulacyjnej
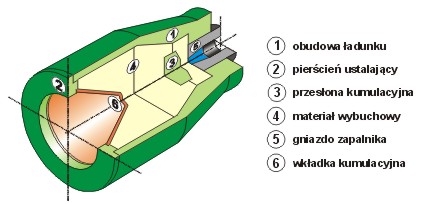
W Zakładzie Technologii i Eksploatacji Uzbrojenia już od początku lat 90-tych prowadzone były intensywne badania w tym zakresie, które zaowocowały szeregiem opracowań dotyczących technologii wytwarzania wkładek kumulacyjnych, ale także poświęcono uwagę na takie zagadnienia jak wpływ kształtu wkładki kumulacyjnej na charakterystyki strumienia kumulacyjnego, roli materiału przesłony inercyjnej czy rodzaju i jakości materiału wybuchowego. Przykładowo na rysunku 2 przedstawiono wkładki kumulacyjne, których materiał podczas procesu wytwarzania poddawany był różnemu stopniowi zgniotu.
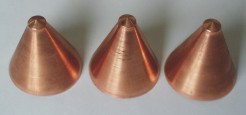
o różnym stopniu zgniotu
Z przeprowadzonych badań nad tak przygotowanymi wkładkami kumulacyjnymi wynika, że stopień odkształcenia plastycznego (zgniot) ma wpływ na charakterystyki penetracyjne strumienia kumulacyjnego i przyjmuje wartość optymalną dla danego materiału wkładki. Przykładowe wyniki tych badań przedstawiono na rysunku 3.
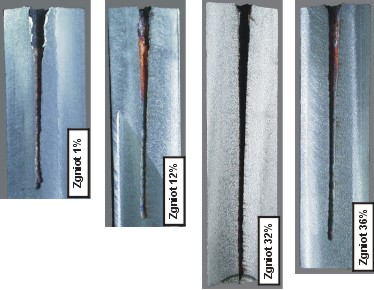
z wkładkami wykonanymi z materiałów o różnym stopniu zgniotu
Z kolei na rysunku 3a przedstawiono zdjęcia rentgenowskie poszczególnych faz formowania się strumienia kumulacyjnego generowanego z laboratoryjnego ładunku kumulacyjnego wyposażonego we wkładkę półsferyczną.
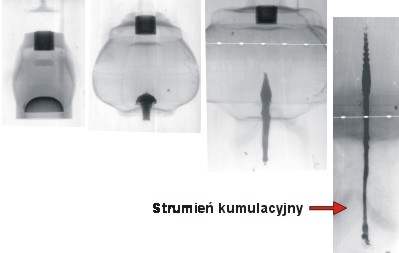
z wkładki półsferycznej
W porównaniu z wkładkami stożkowymi strumień generowany z wkładki półsferycznej jest wolniejszy, ma większą średnicę i posiada większą masę, dzięki czemu jest mniej wrażliwy na zewnętrzne zakłócenia powstałe na przykład w wyniku oddziaływania pancerza reaktywnego. Na rysunku 4 przedstawiono z kolei wyniki badań nad wpływem kształtu wkładki na właściwości penetracyjne ładunków. Wynika z nich, że najgłębiej penetrują strumienie generowane z wkładek stożkowych, jednakże największą objętość i średnicę otworu wlotowego mają kratery powstałe w wyniku oddziaływania strumienia powstałego z wkładki półsferycznej.
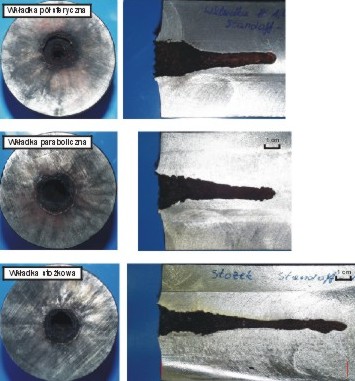
Interesujące wyniki dostarczyły także badania dotyczące roli rodzaju materiału wkładki. Na przykład na rysunku 5 przedstawiono rentgenogramy strumieni generowanych ze spieków miedzi i żelaza. Na podstawie tych zdjęć można stwierdzić, jak rodzaj materiału wkładki silnie wpływa na kształt i strukturę strumienia kumulacyjnego, a w konsekwencji na jego zdolność do penetracji pancerza stalowego.
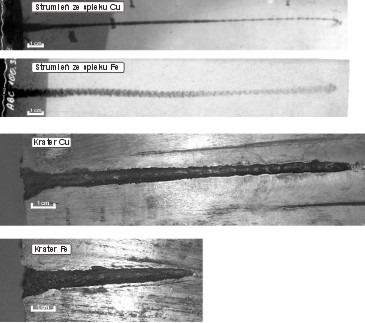
W wyniku kilkuletnich prac naukowo-badawczych pracownicy naukowi zakładu we współpracy z Zakładem Materiałów Wybuchowych zdobyli bardzo duże doświadczenie w zakresie zjawiska kumulacji i technologii ładunków kumulacyjnych, co znalazło wyraz w wielu zgłoszeniach patentowych i publikacjach krajowych i zagranicznych.
Badania spieków ciężkich
Od kilkunastu lat w ZWPWiE są prowadzone badania dotyczące opracowania nowych materiałów na osnowie wolframu (tzw. spieków ciężkich), które mogą znaleźć zastosowanie w produkcji rdzeni podkalibrowych pocisków przeciwpancernych.
Celem wykonywanych prac jest uzyskanie wolframowego spieku ciężkiego o właściwościach penetracyjnych jak najbardziej zbliżonych do właściwości zubożonego uranu. Dlatego też podjęto próby związane ze zmianą składu chemicznego tych materiałów oraz procesu ich wytwarzania.
Badania dotyczyły podwyższenia właściwości spieków ciężkich poprzez zastosowanie następujących sposobów modyfikacji procesu wytwarzania spieków ciężkich:
- zastosowanie spiekania rezystancyjnego do wytwarzania spieków ciężkich,
- modyfikacja składu chemicznego spieków ciężkich poprzez zastosowanie dodatku renu,
- wytwarzanie spieków ciężkich z użyciem proszków sferoidyzowanych w strumieniu plazmy.
Obiektem badań były zarówno stosowane już od wielu lat w różnych dziedzinach przemysłu spieki W-Ni-Fe (głównie w aspekcie badania skutków ich deformacji zachodzącej przy różnej szybkości odkształcenia), jak też spieki ciężkie nowszej generacji zawierające ren (W-Re, W-Re-Ni oraz W-Re-Ni-Fe).
Do procesu wytwarzania badanych spieków wykorzystano prasą izostatyczną SO 5-7451, piec silitowo-rurowy oraz piec próżniowy firmy SECO-WARWICK 20 VP-411/14 HV.
Na rysunkach 1 i 2 pokazano zdjęcia tych urządzeń.
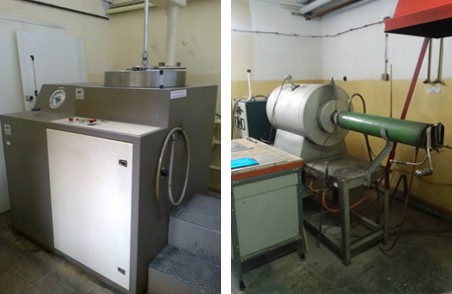
Rys. 1. Urządzenia wykorzystywane podczas badań:
a) prasa izostatyczna SO 5-7451, b) piec silitowo-rurowy
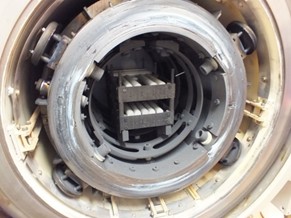
Rys. 2. Komora pieca próżniowego 20 VP-411/14 HV

Rys. 3. Obrazy mikrostruktury wolframowych spieków ciężkich zawierających 5 i 10% Re
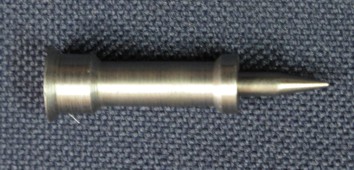
Rys. 4. Pocisk badawczy z rdzeniem wykonanym ze spieku ciężkiego
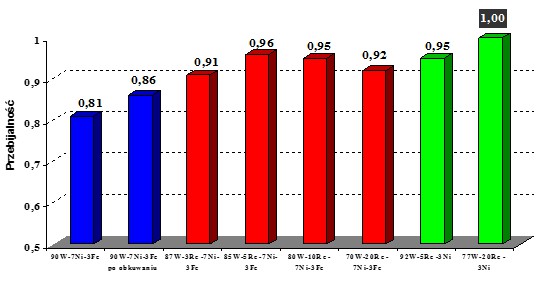
Rys. 5 Wyniki pomiarów przebijalności
Badania mikroskopowe wykazały, że w trakcie penetracji tarcz zachodziło zjawisko tzw. samoostrzenia rdzeni (które również obserwuje się przy strzelaniu rdzeniami ze zubożonego uranu). Wystąpienie tego zjawiska tłumaczyło częściowo tak dobre wyniki uzyskane w badaniach penetracyjnych.
Na rysunku 7 przedstawiono przykładowy obraz krateru z fragmentami rdzenia.
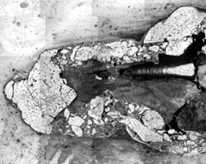
Rys. 7. Obraz metalograficzny części wierzchołkowej krateru z fragmentami rdzenia wytworzonego z mieszanki proszkowej 77W-20Re-3Ni
Sferoidyzacja plazmowa proszków
W ramach realizacji projektu rozwojowego R 00 024 02 oraz innych prac prowadzonych w ZWPWiE wykonano badania możliwości wykorzystania sferoidyzowanych plazmowo proszków wolframu, renu, niklu i żelaza oraz ich mieszanek w procesach wytwarzania spieków ciężkich.
Przeprowadzone badania wykazały, że zastosowanie proszków (np. do wykonywania wolframowych spieków ciężkich) poddawanych uprzednio modyfikacji plazmowej, umożliwia uzyskanie spieków o lepszych właściwościach w stosunku do materiałów wykonanych z proszków wyjściowych. Dokonano analizy możliwości zastosowania tak modyfikowanych proszków do wykonania spieków W-Re, W-Re-Ni i W-Re-Ni-Fe.
Proszki sferoidyzowane mogą również znaleźć zastosowanie w nowoczesnych metodach wytwarzania (rapid prototyping, np. SLS).
Na rysunku 1 przedstawiono schemat blokowy procesów sferoidyzacji plazmowej proszków elementarnych i mieszanek proszkowych (W-Re, W-Re-Ni i W-Re-Ni-Fe), z których w kolejnych etapach realizacji badań wytwarzano spieki ciężkie.
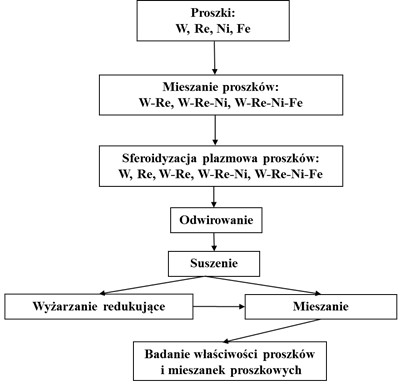
Rys. 1. Schemat blokowy procesów sferoidyzacji plazmowej proszków
Badania sferoidyzacji plazmowej proszków i mieszanek proszkowych przy zastosowaniu stanowiska do natryskiwania plazmowego produkcji Instytutu Badań Jądrowych w Świerku.
Proszek był transportowany do palnika plazmowego w postaci zawiesiny fluidalnej w argonie. Po przejściu przez łuk plazmowy proszek był kierowany do komory wypełnionej argonem i wpadał do pojemnika z wodą destylowaną, gdzie ulegał szybkiemu ochłodzeniu. Schemat stanowiska do modyfikacji plazmowej proszków przedstawiono na rysunku 2.
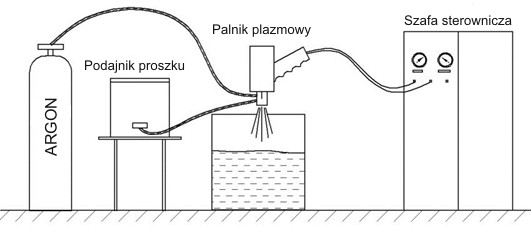
Rys. 2. Schemat stanowiska do sferoidyzacji proszków i mieszanek proszkowych
Procesowi modyfikacji poddawano zarówno proszki metali, jak i mieszanki proszków. Zdjęcia przykładowej proszku renu oraz mieszanki (95W-5Re) po sferoidyzacji zamieszczono na rysunkach 3 i 4.
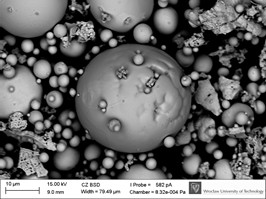
Rys. 3. Cząstki proszku renu – po sferoidyzacji 25kW (pow.3600x)
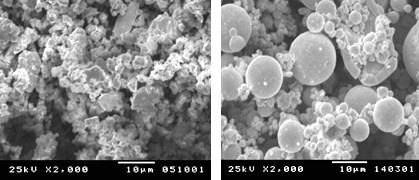
Rys. 4. Proszki mieszanki 95W-5Re przed- i po sferoidyzacji plazmowej (pow. 2000x)
Badanie dynamicznych właściwości mechanicznych

W związku z tym konieczne staje się badanie właściwości mechanicznych materiałów w warunkach dynamicznego odkształcenia. Jedną z metod umożliwiającą badanie właściwości dynamicznych materiałów jest metoda pierścieniowa (ang. expanding ring test). Istota metody pierścieniowej polega na rejestracji radialnego ruchu lub promieniowej prędkości rozszerzania się cienkiego pierścienia, napędzanego produktami detonacji cylindrycznego (kulistego) ładunku materiału wybuchowego lub silnym impulsowym polem elektromagnetycznym.
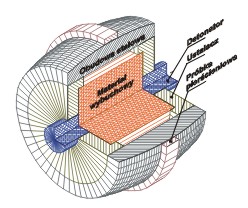
Przy osiowosymetrycznym, dynamicznym rozszerzaniu się cienkiego pierścienia, realizowany jest w przybliżeniu jednoosiowy stan naprężenia. W procesie swobodnego rozszerzania się pierścienia (pod wpływem siły bezwładności) pojawia się rozciągające naprężenie obwodowe, które hamuje jego ruch. Naprężenia obwodowe można określić z wzoru

Z kolei odkształcenie względne, w funkcji naprężenia, zgodnie z definicją, wyznacza się z wyrażenia:

W Zakładzie Technologii i Eksploatacji Uzbrojenia zmodyfikowano metodę pierścieniową, tak aby warunki odkształcania próbki pierścieniowej zbliżyć do tych jakie występują podczas generacji strumienia kumulacyjnego (rys. 3).
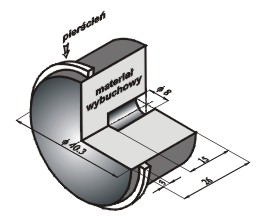
Do rejestracji ruchu radialnego pierścienia zastosowano rentgenograf firmy ScandiFlash, który realizuje technikę rentgenografii impulsowej. Rentgenowski układ pomiarowy przedstawiono na rysunku 4.
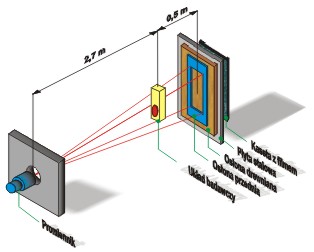
W celu wyznaczenia zmiany wartości promienia pierścienia w całym zakresie jego ruchu do momentu fragmentacji, wykonywane są próby na kilkunastu ładunkach, stosując różne czasy opóźnienia rejestracji. Ponadto, aby otrzymane wyniki były wiarygodne, szczególną uwagę zwraca się na podobieństwo wymiarowe użytych układów badawczych. W wyniku przeprowadzenia szeregu prób wybuchowych otrzymywane są zdjęcia, na których widoczny jest pierścień w różnych fazach wybuchowego rozpęczania (rys. 5).
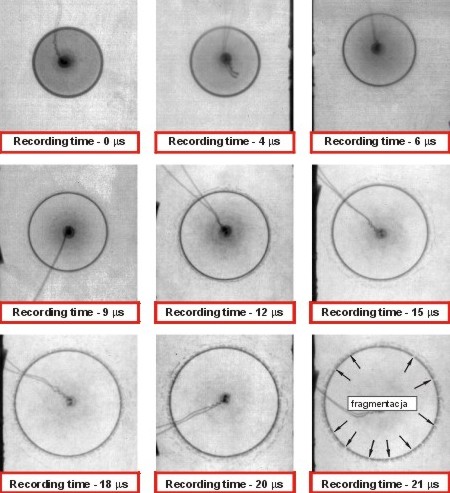
Na podstawie otrzymanych zdjęć można określić podstawowe parametry określające właściwości wytrzymałościowe i plastyczne. W dotychczasowych badaniach, które dotyczyły materiałów stosowanych na wkładki kumulacyjne (różne gatunki miedzi i jej spieków), metodę pierścieniową wykorzystywano przede wszystkim do określania ich właściwości plastycznych (rys. 6).
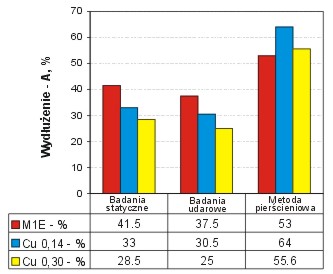
Interesującym wnioskiem wynikającym z analizy powyższego zestawienia jest fakt, iż badane materiały wykazują wyższe właściwości plastyczne (duże wydłużenie) w warunkach badań metodą pierścieniową w porównaniu z badaniami statycznymi i udarowymi. Ponadto zauważono szczególnie wysokie właściwości plastyczne spieku charakteryzującego się małą zawartością zanieczyszczeń (spiek Cu0,14) w warunkach wybuchowego odkształcenia plastycznego. Metoda pierścieniowa to stosunkowo prosty sposób określania właściwości dynamicznych materiałów. Pomimo swych wad (np. niemożliwość zapewnienia stałej szybkości odkształcenia) wyniki uzyskane za pomocą metody pierścieniowej z rejestracją rentgenograficzną mogą stanowić podstawę doboru materiałów na wkładki kumulacyjne i inne elementy broni i amunicji, które poddawane są obciążeniom wybuchowym.
Inżynieria odwrotna
![]() |
![]() |
![]() |
![]() |
![]() |
Zużyty element zawieszenia samochodowego
|
|
Model przestrzenny opracowany na podstawie wyników skanowania
|
|
Zmodyfikowania kopia elementu zawieszenia
|
Nowoczesne metody inżynierii odwrotnej są stale doskonalone. Przede wszystkim unowocześniane są digitizery, za pomocą których dokonuje się przestrzennego pomiaru kształtu. Pomiar ten wykonuje się dwiema metodami bezkontaktową i kontaktową. W metodzie kontaktowej narzędzie pomiarowe „dotyka” bezpośrednio powierzchni mierzonego obiektu. Przykładem digitizera pracującego na takiej zasadzie jest współrzędnościowa maszyna pomiarowa. W metodzie bezkontaktowej, do pozyskiwania informacji na temat geometrii obiektu wykorzystywany jest sygnał pomiarowy w postaci fali świetlnej, dźwiękowej lub elektromagnetycznej. Metoda ta jest bardzo popularna. Znalazła zastosowanie w różnych gałęziach przemysłu, medycynie, architekturze, sztuce. Przykłady urządzeń wykorzystujących metodę bezkontaktową to różnego rodzaju skanery optyczne (pracujące na zasadzie projekcji strukturalnego światła białego lub emisji wiązki promieniowania laserowego), ultrasonografy, tomografy. Wśród urządzeń służących do akwizycji danych o geometrii mierzonego obiektu dużą popularnością cieszą się skanery laserowe. Zasada pracy takiego digitizera, polega na analizie odbitej wiązki promieniowania laserowego wyemitowanej w kierunku mierzonego obiektu. Na podstawie zarejestrowanego przez czujnik sygnału pomiarowego określane są współrzędne punktów odwzorowujących geometrię obiektu rzeczywistego. Proces skanowania, w zależności od rozwiązań konstrukcyjnych zastosowanych w budowie skanera, może odbywać się różnymi metodami. Najczęściej spotyka się skanowanie obrotowe i płaszczyznowe (rys. 2).
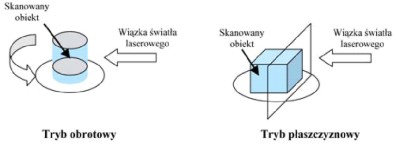
Skanery laserowe mają wiele możliwości w zakresie pozyskiwania informacji o geometrii mierzonych obiektów. Poprzez współpracę z komputerami wyposażonymi w odpowiednie aplikacje istnieje możliwość szybkiego tworzenia modeli 3D (bez konieczności modelowania w środowisku CAD). Na wyposażeniu laboratorium Zakładu Technologii i Eksploatacji Uzbrojenia znajduje się skaner laserowy LPX-250 firmy Roland (rys. 3), który między innymi został wykorzystany do wykonania funkcjonalnego modelu rękojeści nowo zaprojektowanego karabinka maszynowego.
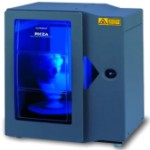
Jako wzorzec kształtu rękojeści, zastosowano plastelinowy model, który powstał w wyniku odciśnięcia dłoni w przygotowanym bloku plasteliny zamocowanej na drewnianym statywie (rys. 4).
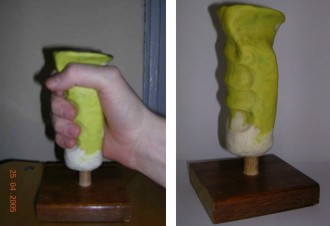
Proces tworzenia modelu 3D rozpoczyna się od operacji digitalizacji, czyli cyfrowego zapisu geometrii rękojeści w postaci współrzędnych punktów x, y, z. W ten sposób otrzymuje się tzw. „chmurę punktów” (rys. 5), na podstawie której można utworzyć powierzchnię poligonalną złożoną z elementarnych trójkątów, odzwierciedlającą geometrię mierzonego obiektu.
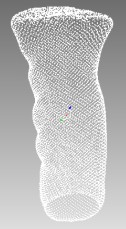
Bardzo często zdarza się, że w trakcie procesu skanowania powstają błędy zniekształcające powierzchnię poligonalną. Ich ilość zależy od rodzaju materiału, z jakiego wykonany jest skanowany przedmiot, jego zdolności do tworzenia refleksów oraz pochłaniania promieniowania laserowego. W celu eliminacji ewentualnych błędów ułożenia punktów stosuje się specjalne systemy komputerowe pozwalające edytować istniejącą chmurę punktów i modyfikować zarejestrowany kształt. (rys.6).
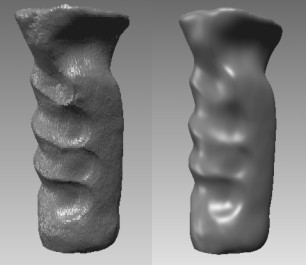
Ze skanerami laserowymi współpracuje wiele aplikacji wyposażonych w funkcje edytowania i optymalizowania otrzymanej powierzchni poligonalnej. Programy takie umożliwiają m.in. łączenie kilku chmur punktów w jedną, wypełnianie obszarów nieciągłości, wygładzanie powierzchni i usuwanie błędnych punktów. Końcowy etap tworzenia modelu powierzchniowego to pokrywanie siatki poligonalnej elementarnymi płatami powierzchni typu NURBS. Każdy płat opisany jest za pomocą określonej liczby punktów kontrolnych, która decyduje o jakości dopasowania płata do odpowiedniego fragmentu siatki poligonalnej. Otrzymany w ostatniej fazie procesu przetwarzania model powierzchniowy może być eksportowany za pomocą różnych formatów wymiany danych CAD takich jak: *.IGES, *.STL, *.DXF. Zapis w wymienionych formatach umożliwia dalszą pracę z modelem 3D w środowisku programów typu CAD (np. Solid Edge, Solid Works, CATIA, Inventor, Rhino, itp.), w celu opracowania modelu bryłowego (rys. 7).
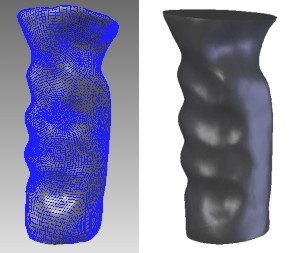
Na podstawie modelu bryłowego rękojeści opracowano następnie kod maszynowy na 5-cioosiową frezarkę sterowaną numerycznie. Na podstawie opracowanego programu obróbkowego wykonano rękojeść z tworzywa epoksydowego (rys. 8).
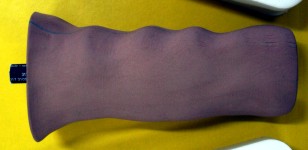
W celu powielenia otrzymanej rękojeści wykonano dodatkowo formę silikonową do odlewania grawitacyjnego części. Widok formy i rękojeści przedstawiono na rysunku 9.
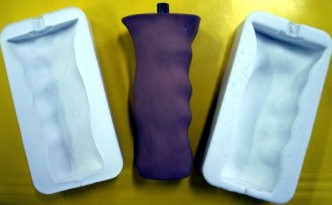
Dzięki tak przygotowanej formie wykonano rękojeść z żywicy poliuretanowej (rys.10), której wytrzymałość jest na tyle wysoka, że może być ona zamocowana w prototypowym karabinku maszynowym.
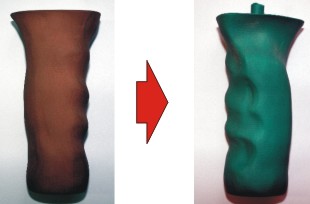
Na podstawie wyżej przedstawionego przykładu zademonstrowano możliwości technologii inżynierii odwrotnej, która znajduje przede wszystkim zastosowanie w kopiowaniu części maszyn, których kształtu nie można opisać za pomocą podstawowych brył geometrycznych.
Opis stanowiska Badań
- zmęczenie cieplne charakteryzujące się cyklicznym działaniem na powierzchnię przewo-du gorących gazów prochowych, powodujących pękanie i odpryskiwanie warstwy chromu oraz przemiany strukturalne w stali;
- tarcie ze znacznym obciążeniem powierzchni podczas odkształcania płaszcza pocisku wcinającego się w gwint lufy. Rozkład obciążenia jest zarówno osiowy wzdłuż przewodu jak i kątowy związany z nadawaniem prędkości obrotowej;
- erozja gazowa polegająca na wymywaniu materiału lufy przez kinetyczne oddziaływanie strumienia gorących gazów prochowych;
- zmęczenie materiału lufy krótkotrwałymi cyklicznymi impulsami obciążenia podczas strzelania działającymi w zakresie odkształceń sprężystych;
- zniszczenie chemiczne poprzez utlenianie i odkładanie produktów powstających podczas niepełnego spalenia prochu.
Wykonanie badań o takim zakresie jest kosztowne, ponieważ mogą być prowadzone tylko w wyspecjalizowanych ośrodkach, wymagają zużycia sporej ilości amunicji oraz zastosowania specjalistycznego sprzętu. A co najważniejsze, wyniki badań niszczących nie mogą służyć do bieżącego monitorowania przebiegu eksploatacji. W Instytucie Elektromechaniki WAT w ramach prac prowadzonych we współpracy z Zakładami Metalowymi Łucznik skonstruowano nowy system broni strzeleckiej kalibru 5,56 [mm] wz. 331. W przypadku tej konstrukcji zaistniała unikalna szansa prześledzenia zjawisk zużycia przewodu lufy na etapie odbiorczych badań trwałościowych prototypu. W tym celu skompletowano stanowisko (rys.1) do nieniszczącego przeglądania przewodów luf po różnym ostrzale i zarejestrowano materiał badawczy, który posłużył do przetestowania stopnia przydatności zaproponowanej metody do monitorowania przebiegu eksploatacji oraz kierunku dalszych prac przy udoskonalaniu stanowiska.
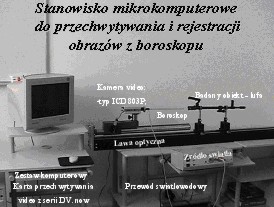
Podstawowymi parametrami, jakimi powinien charakteryzować się taki przyrząd to:
- niewielka średnica końcówki wziernika poniżej 5 [mm];
- krótka ogniskowa, aby obserwować blisko położony przewód lufy;
- kąt obserwacji zbliżony do 90 [o];
- możliwie duża głębia ostrości, bez zniekształceń optycznych;
- możliwie rozproszone światło wiązki oświetlającej z możliwością redukcji odbłysków od przewodu lufy;
- długość przekraczająca przeciętną długość lufy broni strzeleckiej (około 600 [mm]);
- możliwie sztywna konstrukcja umożliwiająca swobodne przemieszczanie się końcówki wziernika w przewodzie lufy;
- możliwość sprzężenia wziernika z kamerą, bądź cyfrowym aparatem fotograficznym;
- możliwość łatwego montażu i demontażu na ruchomym wysięgniku.
Na podstawie opisanych wyżej parametrów oraz przedstawionych ofert dokonano wyboru, a zakupiony boroskop charakteryzował się następującymi parametrami:
- średnicą 4,1 [mm];
- kątem obserwacji 70 [o];
- długością 280 [mm];
- ogniskową 1-3 [mm].
Do rejestracji obrazu wytypowano kamerę CCD (ang. Charge Coupled Devices) prod: Ike-gami typ ICD 803P, z dopasowanym adapterem umożliwiającym zamocowanie boroskopu oraz obserwowanie obrazu (rys.1) na monitorze. Boroskop z kamerą został umocowany do ramienia umożliwiającego ruch posuwisto-zwrotny, całość ustawiono na ławie optycznej, aby zapewnić współosiowość przyrządu z lufą. Aby uzyskać jak najwięcej informacji opracowano specjalną metodykę badań. Ponieważ ba-dane lufy były większej długości niż boroskop, obserwacje przeprowadzono z obu stron, przesuwając końcówkę przyrządu z niewielką prędkością tak, aby uchwycić zmiany eksplo-atacyjne na całej długości. Dodatkowo obracając końcówką boroskopu w zakresie 360[o] obserwowano miejsca nara-żone na największe zużycie: początek bruzd i miejsce gdzie następuje rozcalenie pocisku z łuską oraz ujście przewodu gazowego.
![]() |
![]() |
![]() |
Rys.2a
|
Rys.2b
|
Rys.2c
|
![]() |
![]() |
![]() |
Rys.2d
|
Rys.2e
|
Rys.2f
|
![]() |
![]() |
Rys.3a
|
Rys.3b
|
![]() |
![]() |
Rys.3c
|
Rys.3d
|
W dalszej części pracy wykorzystano zarejestrowane obrazy do opisu ilościowego, ponie-waż dopiero taka analiza pozwala na określenie zależności nasilenia zużycia przewodu lufy od ostrzału konkretnym rodzajem amunicji. Digitalizacja, mimo że nie wprowadza znaczącej utraty jakości, to także nie doprowadza do zadawalającej postaci „zatrzymanego obrazu”. Jedynie eliminując pośredni etap digitalizacji obrazu analogowego możemy uzyskać możli-wość oceny ilościowej zużycia luf. Istota problemu wydaje się tkwi w ograniczonych możli-wościach poprawienia jakości sygnału analogowego. Ilościowe ujęcie zużycia powierzchni przewodów luf broni małokalibrowej powinien zmie-rzać w kierunku wykorzystania cyfrowej techniki przechwytywania i rejestracji obrazów (rys.4a i rys.4b). Niewątpliwą dodatkową zaletą przejścia na cyfrową technikę rejestracji (rys.4a) jest znaczne zwiększenie użyteczności uzyskiwanego obrazu poprzez możliwość wykonywania zbliżeń (rys.4b) i innych efektów bez jakiejkolwiek utraty jakości.
![]() |
![]() |
Tak zarejestrowany obraz jest dalej przetwarzany a jego jakość umożliwia ilościowy opis zjawiska zużycia przewodów luf z zastosowaniem cyfrowej obróbki sygnału np. z zastosowa-niem oprogramowania (LUCIA).
Zakres pracy badawczej statutowej (PBS) prowadzonej w Zakładzie
- Pierwsza, o numerze P0003/2 z wersji podstawowej karabinka, która przeszła cały cykl badań trwałościowych i wystrzelono z niej 10 000 szt. amunicji produkcji Hirtenberger.
- Druga, o numerze P0003/1 z wersji podstawowej karabinka, która przeszła cały cykl badań trwałościowych i wystrzelono z niej 10 000 szt. amunicji produkcji MESKO.
- W trakcie badań trwałościowych określano spadek prędkości wylotowej i skupienie pocisków w celu.
W celu wykonania metalograficznego badania zużycia przewodów luf, po próbach trwałościowych, z zastosowaniem mikroskopii optycznej i elektronowej, lufy kaliber 5,56 o numerach 0003/2 i 0003/1 pocięto na próbki w następujący sposób:
- Lufę o numerze P0003/2 poprzecznie do osi na 6 odcinków o dł. po 82mm, a następnie wzdłużnie aby odsłonić przewód lufy.
- Lufę o numerze P0003/1 poprzecznie do osi na 6 odcinków o dł. po 83mm, a następnie wzdłużnie aby odsłonić przewód lufy.
![]() |
![]() |
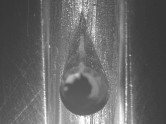

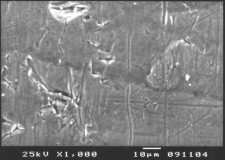
- W lufach stwierdzono dwie strefy o nasilony zużyciu; opierwszą obszarze powyżej miejsca rozcalenia pocisku z łuską, drugą w pobliżu przewodu gazowego.
- W pierwszej strefie zjawiskiem, które w dominujący sposób przyczynia się do zniszczenia powłoki chromu są przemiany strukturalne stali spowodowane wysoką temperaturą gazów prochowych (powyżej 730 oC) oraz utlenianiem odsłoniętej powierzchni.
- W lufie P0003/2 , w której stosowano amunicję Hirtenbergera zniszczenia są wyraźnie mniej-sze, co prawdopodobnie wynika z niższej temperatury gazów prochowych tylko nieznacznie przekraczającej 730 oC.
- Zniszczenia przewodu lufy P0003/1, w której stosowano amunicję MESKO są większe i dalej posunięte. W tym przypadku zaobserwowano poza zniszczeniem powłoki chromowej, także intensywne utlenianie odsłoniętej powierzchni stali i jej łuszczenie. Prawdopodobnie wynika to z wyższej temperatury gazów prochowych i ich bardziej agresywnego składu chemicznego.
- Sam mechanizm niszczenia powłoki chromowej w obu lufach jest podobny zachodzi tylko z większą intensywnością w lufie P0003/1, strzelanej amunicją MESKO.
- W strefie wokół przewodu gazowego zjawiskiem niszczącym jest erozja gazowa.
- Zniszczenia przewodu lufy w strefie pierwszej są znacznie większe niż w strefie drugiej i na-leży przypuszczać, że to one mają największy wpływ na spadek prędkości wylotowej pocisku.
- Sposobem na zwiększenie trwałości przewodów luf jest wprowadzenie zmian materiałowych polegających na zastąpieniu dotychczas stosowanych stali takimi, w których podczas nagrze-wania nie zachodzi przemiana strukturalna ferrytu w austenit Takimi stalami są między inny-mi stale austenityczne.
Pracownia badań właściwości mechanicznych materiałów w warunkach dynamicznego obciążenia
- Opis pracowni oraz prowadzonych badań
- Film 2 – Test brazylijski
- Film 3 – Test Taylora PA-4
- Film 4 – Taylor AISI 321
- Film 5 – Symetryczny
- Film 6 – Ekspansja pierścienia
- Film 7 – Parafina